Internet of Things in Oil & Gas has been saved
Perspectives
Internet of Things in Oil & Gas
Explore use cases and perspectives
The Internet of Things (IoT) in the oil & gas industry is the network of physical objects connected to the Internet. Wearable devices, vehicles, equipment, buildings, and just about any other thing can be embedded with electronics, software, sensors, and network connectivity. The ability to transfer data without requiring human interaction enables previously unprecedented amounts of data to be collected and exchanged with other devices, or through a central platform. Increasingly, forward-thinking oil & gas organizations are focusing their IoT initiatives less on underlying sensors, devices, and "smart" things and more on developing bold approaches for managing data, leveraging "brownfield" IoT infrastructure, and developing new business models.
Explore content
- Sensor-based tank monitoring
- Acoustic operations monitoring
- Digital twin for projects
- Digital twin for assets
- Seismic exploration sensors
Sensor-based tank monitoring
Sensors provide data for cloud-based digital dashboards to monitor real-time equipment performance and inventory levels in the oil & gas industry
In the oil & gas industry, sensors that monitor inventory levels of onshore oil tanks automatically dispatch trucks when the tanks need to be emptied. Sensors also monitor the performance of above-ground pumps to alert maintenance teams of potential and actual issues, and provide employees with early warning signs of possible safety issues to help prevent injuries and fatalities. Real-time oil tank sensor notifications enable continuous pumping while optimizing inventory transportation and minimizing downtime costs. Cloud-based digital dashboard visualizations convey information in an insightful manner that drives improved decision-making.
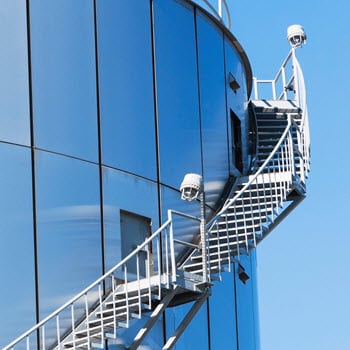
Acoustic operations monitoring
Sensors continuously measure oil composition and flow rates to reduce expensive equipment use
Inexpensive IoT acoustic sensors in the oil field continuously analyze oil composition (oil, water, gas, etc.) within pipelines, while laboratory tests from simulated field conditions and selected sensors exhibiting optimal oil flow performance enhance the readings. In addition, statistical models estimate the composition and flow rates to continuously improve planning for subsequent operations and reduce expensive equipment use.

Digital twin for projects
Digital replicas of physical assets simplify change analysis
A fully loaded digital twin–a digital replica of an actual asset being constructed–gives oil & gas companies the ability to drill down virtually to obtain project progress updates (e.g., outstanding issues, bottleneck constraints) increasing knowledge-gathering efficiency. The digital twin also provides a 3D status report that allows management to "look around the platform" and understand the status of each component from design, to build, to assembly. Information is fed into a dashboard that tracks real-time actuals at the part and component level and compares outputs against historical performance. Constructing a digital twin can improve project speed and quality, and provide insights into process and design improvement opportunities in the oil & gas industry.
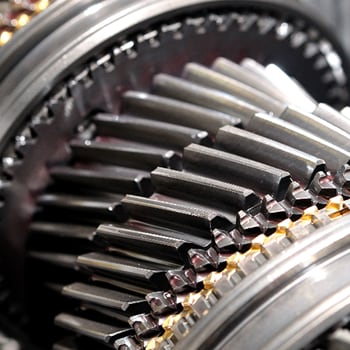
Digital twin for assets
Digital replicas of physical assets improve maintenance operations
Maintaining the digital twin developed during asset construction (e.g., upgrades, equipment changes, etc.) can improve asset management and performance for oil & gas companies. A digital twin predicts potential maintenance issues and optimizes operating parameters to elongate asset life and reduce downtime. Problems can be resolved quickly by drilling down into the digital twin to understand the issue and formulate a repair plan. In addition, comparing performance across assets and executing root-cause analyses helps to improve evidence-based asset management. These benefits can be expanded by using a visual- or virtual reality-based digital twin.
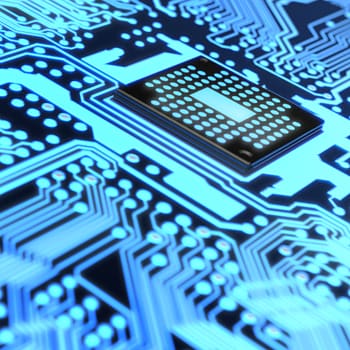
Seismic exploration sensors
Seismic sensors aid oil exploration
Individual IoT sensors connected by fiber optic cables aid oil exploration by mapping subsurface drilling sites to determine new drilling locations and optimize output of operational sites. An Internet-connected seismic sensor network collects data (over a million readings per site) and transfers it to servers to provide an image of the subsurface site. Comparative data analysis is conducted to select the best drilling site. The sensor-based system improves the new and existing drilling rig productivity and reduces the time required for site-selection data analysis.
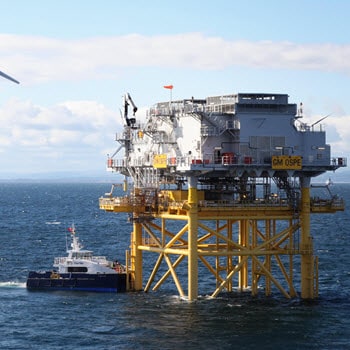
IoT refreshes pipeline asset management
A midstream company was struggling with asset management lifecycle challenges as its aging infrastructure created competing investment priorities. They wanted to refocus their program on leveraging data to improve information management, predictive asset management, asset risk management, and asset management planning.
Discover how we refreshed multiple dimensions of the program using the Internet of Things (IoT) and data-driven approaches.
Using IoT connectivity to drive differentiation
Even if your devices and products look the same as they did before they got smart and connected, they’re fundamentally different—now they’re members of a larger community of products, processes, and stakeholders. Making objects capable of filling those new roles is a serious design challenge.